AC vs. DC Servo Motors: The Ultimate Guide
Imagine a robotic arm smoothly picking and placing components with pinpoint accuracy, or a CNC machine carving intricate designs in metal. These feats of precision engineering rely on servo motors, the unsung heroes of automation. But not all servo motors are created equal. This guide dives deep into the world of servo motors, exploring the critical distinctions between AC and DC variants, empowering you to choose the perfect motor for your next project.
Understanding the difference between AC and DC servo motors is crucial for anyone working with automated systems. These motors are the muscle behind precise motion control, and selecting the right type can significantly impact performance, cost, and overall system efficiency. Whether you're a seasoned engineer or just starting out, this guide will provide you with the knowledge to make informed decisions about servo motor selection.
The need to distinguish between AC and DC servo motors stems from their inherent design differences, leading to varying performance characteristics. DC servo motors have been around longer, offering simple control and high starting torque. However, AC servo motors have gained popularity due to their brushless design, resulting in higher speeds, lower maintenance, and better power handling capabilities. Comparing these motor types allows engineers to tailor their choice to the specific demands of the application.
Historically, DC servo motors dominated the automation landscape due to their simplicity and affordability. However, the advent of advanced power electronics and control systems has propelled AC servo motors to the forefront, particularly for high-performance applications. The ongoing development of motor technology and control algorithms continues to refine the performance and capabilities of both AC and DC servo motors.
A servo motor is a rotary actuator or linear actuator that allows for precise control of angular or linear position, velocity, and acceleration. It consists of a suitable motor coupled to a sensor for position feedback. It also requires a relatively sophisticated controller, often a dedicated module designed specifically for use with servo motors. Distinguishing between AC and DC servo motors involves understanding their construction, control methods, and performance characteristics. AC motors utilize a rotating magnetic field generated by three-phase AC power, while DC motors rely on a commutator and brushes to switch the current direction in the rotor windings.
One benefit of understanding the differences is the ability to optimize cost. DC motors are often less expensive upfront. Another benefit is improved performance. AC motors excel in high-speed applications, while DC motors provide high starting torque. Finally, recognizing these distinctions improves maintenance planning. AC motors require less maintenance due to their brushless design.
Advantages and Disadvantages of AC and DC Servo Motors
Feature | AC Servo Motor | DC Servo Motor |
---|---|---|
Speed | High | Moderate |
Torque | High at high speeds | High at low speeds |
Maintenance | Low | High (brush replacement) |
Cost | Higher initial cost | Lower initial cost |
Best Practices:
1. Properly size the motor for the application.
2. Use appropriate control algorithms.
3. Implement proper cooling mechanisms.
4. Regularly monitor performance.
5. Ensure proper grounding and wiring.
Real Examples:
1. Robotics
2. CNC Machines
3. Automated Manufacturing
4. Aerospace applications
5. Medical Devices
Challenges and Solutions:
1. Overheating - Implement cooling solutions
2. Control complexity - Use advanced control systems
3. Cost optimization - Choose the appropriate motor type for the application
4. Noise - Implement noise reduction techniques
5. Vibration - Use vibration dampening methods
FAQs:
1. What is a servo motor?
A servo motor is a motor with position feedback.
2. What are the different types of servo motors?
AC and DC.
3. What are the applications of servo motors?
Robotics, automation, etc.
4. What are the advantages of using servo motors?
Precise control.
5. What are the disadvantages of using servo motors?
Cost, complexity.
6. How to choose a servo motor?
Based on application requirements.
7. How to maintain a servo motor?
Regular inspection and lubrication.
8. What are the future trends in servo motor technology?
Increased efficiency and miniaturization.
Tips and Tricks:
Properly sizing the motor for the application is critical for optimal performance and efficiency. Consider factors like load, speed, and torque requirements when selecting a servo motor. Consult with motor specialists if necessary.
In conclusion, understanding the differences between AC and DC servo motors is crucial for successful automation projects. Each motor type has its own set of advantages and disadvantages, and selecting the right one requires careful consideration of the specific application requirements. By understanding the nuances of each type, you can optimize performance, cost, and maintenance. The ability to differentiate these motors empowers engineers to design more efficient, reliable, and cost-effective automated systems. Take the time to thoroughly analyze your project needs, consult with experts, and leverage the information provided in this guide to make the best decision for your specific application. Investing in the right servo motor will pay dividends in the long run, ensuring smooth, precise, and reliable operation of your automated systems.
Propane furnace condensate drain a comprehensive guide
Unlocking potential proracing obd tuning box guide
Cracking the code small bathroom design 8x7








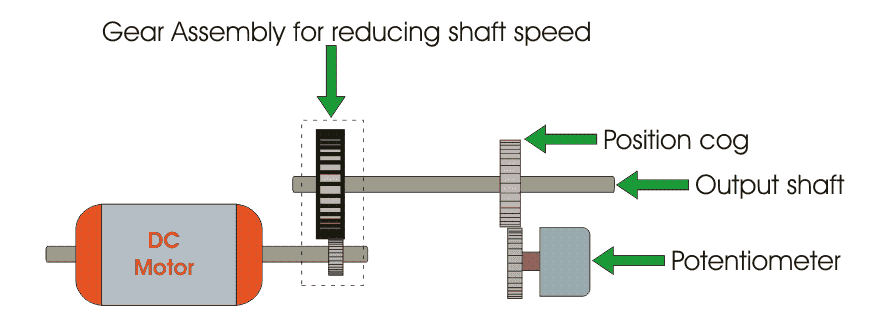

