Sink or Swim: Choosing the Right Bilge Pump Wire Size
Imagine this: you're out on the water, enjoying a perfect day, when suddenly you notice water accumulating in your boat's bilge. You flip on your bilge pump, but nothing happens. A sinking feeling washes over you – literally. One of the most common culprits in bilge pump failure is incorrect bilge pump wiring, specifically, using the wrong wire size. Don't let this happen to you. Understanding bilge pump wire sizing is crucial for keeping your boat afloat and your adventures worry-free.
Selecting the correct wire gauge for your bilge pump isn't just about getting the pump to run; it's about safety and preventing electrical hazards. Using undersized wiring can lead to overheating, voltage drop, and even fire. Oversized wiring, while less dangerous, can be unnecessarily expensive and difficult to work with. This guide will dive deep into the world of bilge pump wiring, ensuring you choose the right gauge for your specific setup.
While the concept of electrical wiring has been around for centuries, the application of specific wire sizes to bilge pumps is more recent, evolving alongside the development of recreational boating and the increasing reliance on electric bilge pumps. In the early days of boating, manual bilge pumps were the norm. However, as boats became more complex and electrically powered systems became prevalent, electric bilge pumps gained popularity, necessitating careful consideration of wire sizing for optimal performance and safety. The importance of correct bilge pump wire sizing cannot be overstated. It directly impacts the pump's efficiency, longevity, and most importantly, the safety of your vessel and passengers.
A key issue related to bilge pump wire size is the potential for voltage drop. Voltage drop occurs when the resistance of the wire causes a decrease in voltage between the power source and the pump. This can significantly reduce the pump's performance, potentially leaving you stranded with a flooded bilge. The longer the wire run and the higher the amperage draw of the pump, the more significant the voltage drop. Therefore, choosing the correct wire size is essential to mitigate this issue.
Understanding wire gauge is fundamental to proper bilge pump wiring. Wire gauge refers to the physical size of the wire, with smaller gauge numbers indicating thicker wires and larger gauge numbers indicating thinner wires. A thicker wire (lower gauge number) has less resistance and can carry more current. For example, a 10-gauge wire is thicker and can carry more current than a 14-gauge wire. The American Wire Gauge (AWG) system is the standard used in the United States for specifying wire sizes.
One major benefit of using the correct bilge pump wire size is increased pump efficiency. With the right gauge wire, the pump receives the necessary voltage and current to operate at its full potential, quickly and effectively removing water from the bilge. Another key advantage is enhanced safety. Properly sized wiring prevents overheating, reducing the risk of fire and protecting your boat and passengers. Lastly, using the correct wire size ensures the longevity of your bilge pump. Consistent and reliable power delivery prevents strain on the motor, extending its lifespan.
To determine the appropriate wire size for your bilge pump, consider the pump's amperage draw, the length of the wire run, and the voltage of your boat's electrical system. Consult the pump manufacturer's specifications for the recommended wire size. You can also use online wire size calculators to help you make the correct selection. Always err on the side of caution and choose a slightly thicker wire (lower gauge number) if you are unsure.
Advantages and Disadvantages of Different Wire Sizes for Bilge Pumps
Wire Size (AWG) | Advantages | Disadvantages |
---|---|---|
10 | Handles high current, minimal voltage drop | Can be stiff and difficult to work with |
12 | Good balance of current capacity and flexibility | May not be suitable for very long runs or high-amp pumps |
14 | More flexible, easier to install | Higher voltage drop potential, limited current capacity |
Best Practices:
1. Consult manufacturer specifications.
2. Use marine-grade wire.
3. Properly fuse the circuit.
4. Use waterproof connectors.
5. Regularly inspect wiring.
Frequently Asked Questions:
1. What happens if I use the wrong wire size? - Overheating, voltage drop, fire hazard, pump malfunction.
2. Where can I find the recommended wire size? - Pump manufacturer specifications.
3. What type of wire should I use? - Marine-grade tinned copper wire.
4. Do I need a fuse? - Yes, always fuse the circuit to protect the pump and wiring.
5. How do I calculate wire size? - Use online calculators or consult a marine electrician.
6. What is voltage drop? - Reduction in voltage due to wire resistance.
7. How can I prevent voltage drop? - Use the correct wire size for the length of the run and amperage draw.
8. How often should I inspect my bilge pump wiring? - At least annually, or more frequently if the boat is used in harsh conditions.
In conclusion, selecting the correct wire size for your bilge pump is a critical aspect of boat maintenance and safety. It ensures efficient water removal, prevents electrical hazards, and prolongs the life of your pump. By following the guidelines outlined in this article, understanding the importance of proper wire sizing, and consulting manufacturer specifications, you can equip your vessel with a reliable bilge pump system that will keep you afloat and worry-free for years to come. Taking the time to carefully select and install the correct wire size for your bilge pump is a small investment that can prevent major headaches and potentially save your boat from disaster. Don't take chances with your safety and the well-being of your vessel – prioritize proper bilge pump wiring and enjoy peace of mind on the water.
Official leslie sansone website
Conquering the concrete jungle the lunar rock rav4 xle premium
Rental contract sample philippines your ultimate guide to stress free leasing






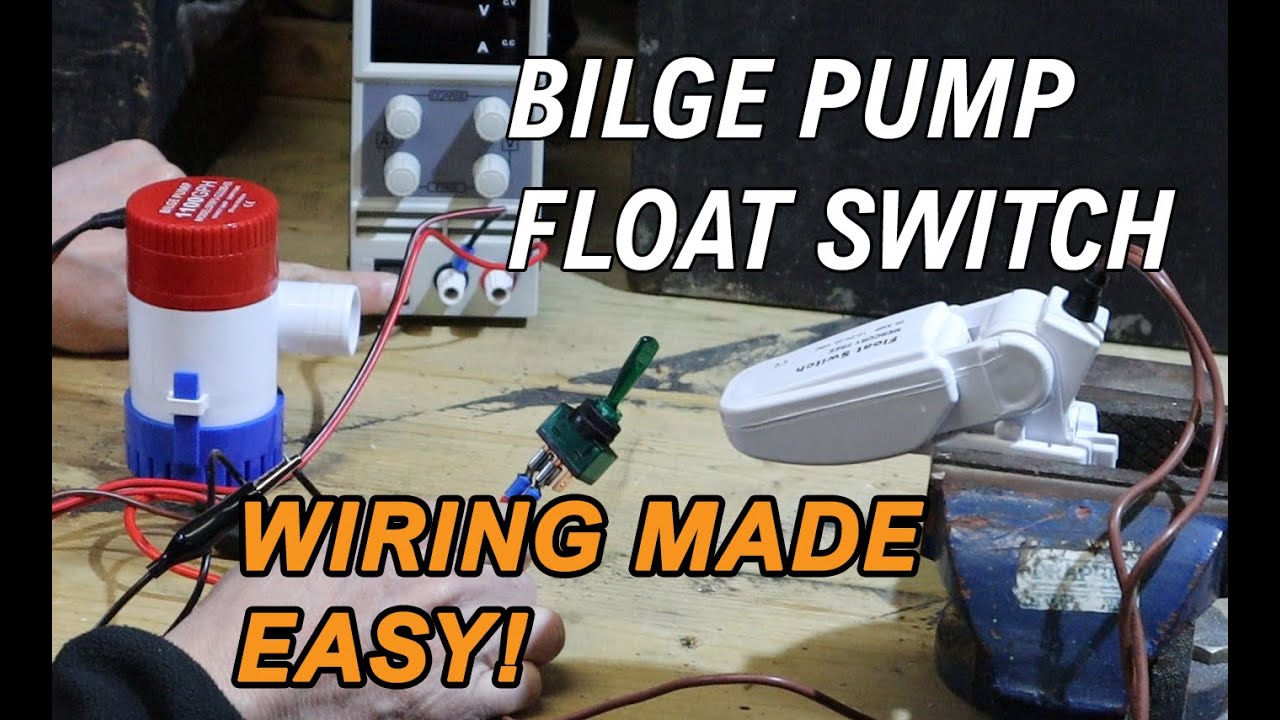


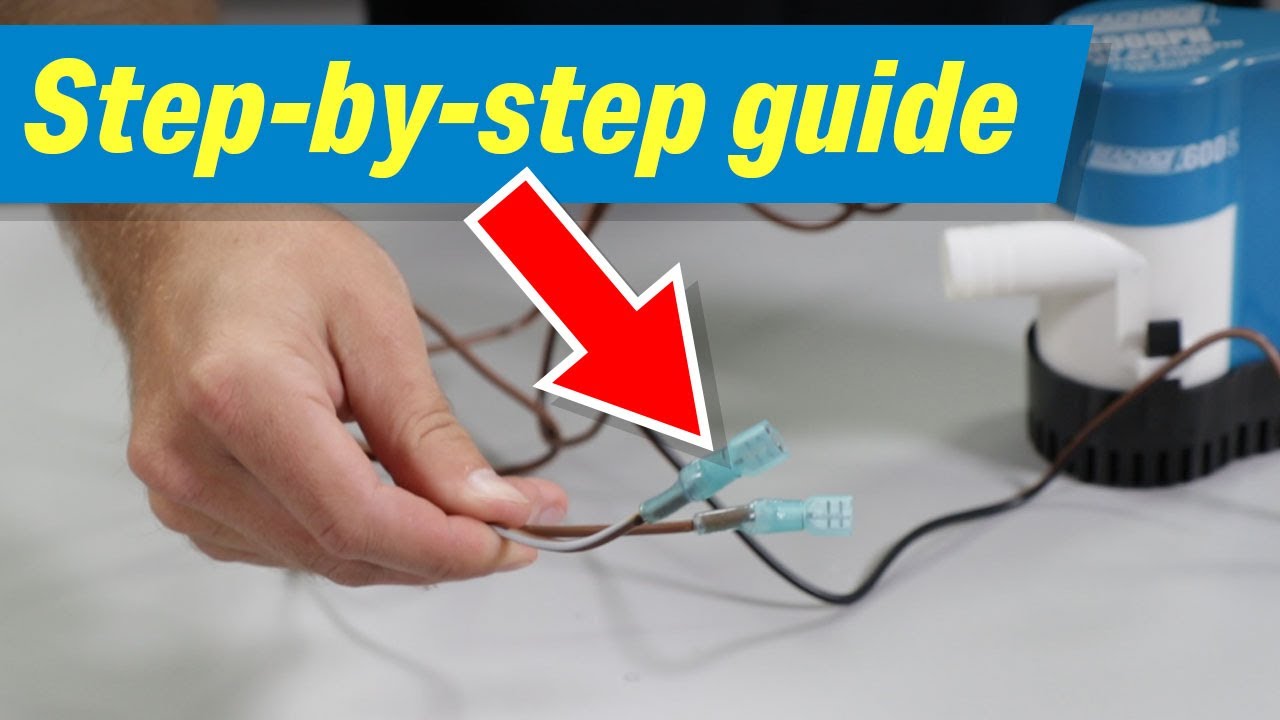




