Unlocking the Secrets of Metric Key Dimensions: Your Guide to Hardware Harmony
Ever find yourself staring blankly at a jumble of screws, bolts, and nuts, wondering which one fits where? It's a universal experience, a rite of passage for anyone who's ever attempted a DIY project or simply tried to assemble flat-pack furniture. But imagine a world where you could instantly identify the correct fastener just by glancing at its dimensions. That's the power of understanding metric key dimensions, the Rosetta Stone of the hardware world.
Metric key sizes, often depicted in handy charts, are a crucial element in ensuring smooth assembly and functionality across various mechanical components. They provide a standardized system for identifying and matching fasteners, eliminating the guesswork and frustration that often accompany projects involving screws, bolts, and keys. From assembling furniture to repairing machinery, a grasp of these dimensions can save you valuable time and prevent costly mistakes.
But how did this system of standardized key sizes come about? The metric system itself is a product of the French Revolution, a radical attempt to bring order and logic to a world of chaotic and inconsistent measurements. This standardization eventually extended to fasteners and keys, leading to the development of the metric key size charts we rely on today. These charts, often presented as comprehensive tables, list various key dimensions, including width, height, and depth, allowing for precise identification and selection.
The importance of these charts cannot be overstated. They are the backbone of modern manufacturing, enabling seamless collaboration and interoperability across industries and countries. Imagine trying to assemble a complex piece of machinery with components sourced from different manufacturers, each using their own unique sizing system. It would be a logistical nightmare! Metric key size charts provide a common language for hardware, ensuring that parts fit together regardless of their origin.
However, even with standardized charts, challenges can arise. One common issue is the potential for misinterpretation or misreading of the charts. A slight error in measurement or a misunderstanding of the units used can lead to selecting the wrong key size, resulting in damaged components or failed assemblies. This highlights the importance of careful attention to detail and the use of accurate measuring tools when working with metric key dimensions.
A simple example illustrating the importance of metric key sizes can be found in the common hex key, also known as an Allen wrench. These keys come in various metric sizes, typically ranging from 1.5mm to 10mm. Using a 4mm hex key on a screw that requires a 5mm key can strip the screw head, making it difficult or impossible to remove. This simple scenario underscores the critical role that accurate key size selection plays in everyday tasks.
One benefit is interoperability. Metric keys are the global standard, enabling compatibility across various manufacturers and industries.
Another advantage is precision. Metric key size charts provide precise measurements, ensuring accurate fit and preventing damage to components. This level of precision is especially critical in industries like aerospace and automotive, where even minor discrepancies can have significant consequences.
Finally, these charts promote efficiency. By providing a standardized system for identification, metric key size charts streamline the assembly process and reduce the time spent searching for the correct fastener.
Advantages and Disadvantages of Standardized Metric Key Sizes
Advantages | Disadvantages |
---|---|
Global standardization and interoperability | Potential for misinterpretation of charts |
Precise measurements for accurate fit | Need for precise measuring tools |
Increased efficiency in assembly processes | Availability of specific sizes might vary regionally |
Frequently Asked Questions:
1. What is a metric key size chart? - A chart showing dimensions of metric keys.
2. Where can I find a metric key size chart? - Online or in engineering handbooks.
3. Why are metric key sizes important? - For accurate fit and component compatibility.
4. What units are used in metric key size charts? - Millimeters.
5. How do I measure a metric key? - With calipers or a metric ruler.
6. What are some common metric key sizes? - 1.5mm, 2mm, 2.5mm, 3mm, 4mm, 5mm, 6mm, 8mm, 10mm.
7. What happens if I use the wrong size key? - Potential damage to the fastener or component.
8. Where can I buy metric keys? - Hardware stores, online retailers.
In conclusion, understanding metric key dimensions is fundamental for anyone working with hardware. From assembling furniture to building complex machinery, the ability to quickly and accurately identify the correct key size is essential. Metric key size charts provide a valuable resource, enabling precision, efficiency, and interoperability across industries. By mastering the information contained within these charts, you unlock a world of possibilities, empowering you to tackle projects with confidence and ensuring that your hardware works in perfect harmony. Take the time to familiarize yourself with these crucial dimensions, and you'll find that the world of hardware becomes a much less daunting place.
Decoding wells fargo checking minimum balance what you need to know
Unveiling the timesheet miracle salad calculator
Decoding federal wage grade pay












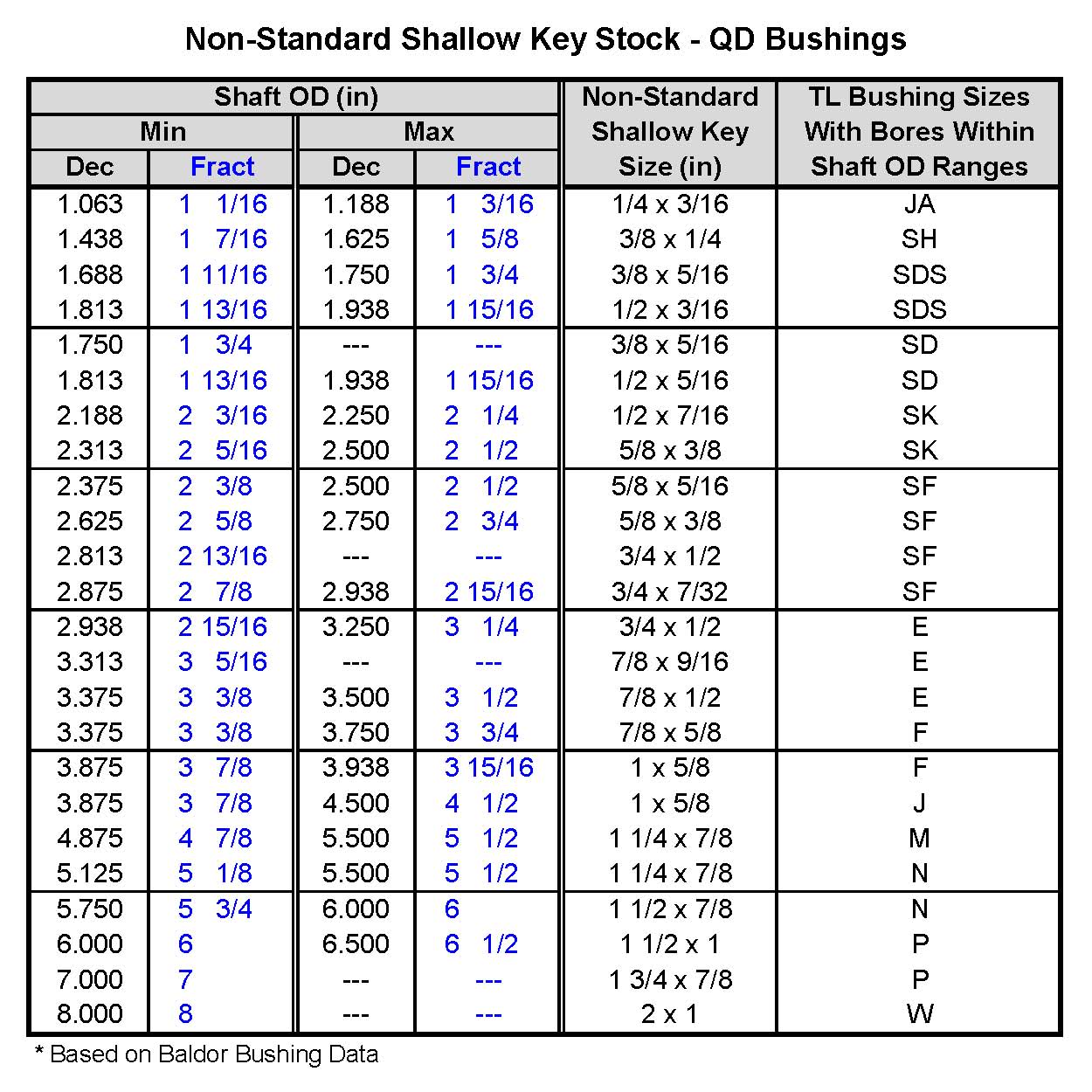